Renewable Energy Inspections
BIOGAS
As the world confronts the pressing challenges of climate change, monitoring emissions from landfills has become a crucial focus area.
Biogas facilities and landfill sites are often expansive, making traditional inspections time-consuming. Drones can cover large areas quickly, making them ideal for tasks like site monitoring of waste decomposition for the assessment of the environmental impact. Drones provide up to date data, accelerating the inspection process compared to ground-based methods.
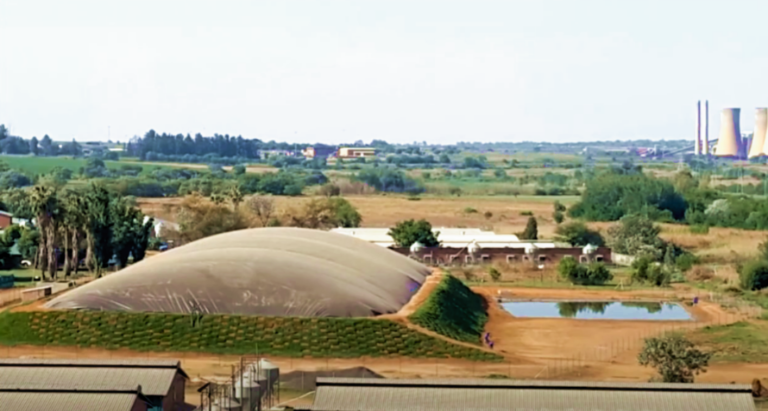
Thermal Imaging for Gas Leak Detection
Methane (CH₄) is a significant byproduct of biogas and landfill sites and its detection is critical for both safety and environmental protection. Drones equipped with thermal imaging cameras or gas sensors, can detect methane leaks or elevated temperatures indicating potential issues with gas flare systems or biogas digesters. Thermal imaging also helps identify areas of concern in gas collection systems.
Air Quality Monitoring and Environmental Assessments
Drones can carry air quality sensors to monitor pollutants such as methane, carbon dioxide (CO₂), volatile organic compounds (VOCs), and other greenhouse gases that are emitted from landfill or biogas sites. By mapping these emissions, drones help facility managers assess the environmental impact of their operations and ensure compliance with environmental regulations.
Precise 3D Mapping and Topography
Drones with LiDAR or photogrammetry capabilities can create accurate 3D models of landfill and biogas sites. This data can be used to monitor the settling or movement of waste materials, assess land erosion, and ensure compliance with regulatory guidelines for waste management. For landfill sites, drones provide valuable data for stockpile management, slope stability, and volume assessments.
SOLAR PV: PRE-EMPTIVE MAINTENANCE INSPECTIONS
As the world confronts the pressing challenges of climate change, monitoring emissions from landfills has become a crucial focus area.
Solar farms span large, remote areas, making traditional inspections time-consuming and labour-intensive.
Drones with thermal cameras quickly detect hot spots or defects, indicating issues like cell damage, shading or malfunctioning diodes that reduce energy output or pose fire risks.
Drone thermal imaging extends panel lifespan, boosts energy production and lowers operational costs.
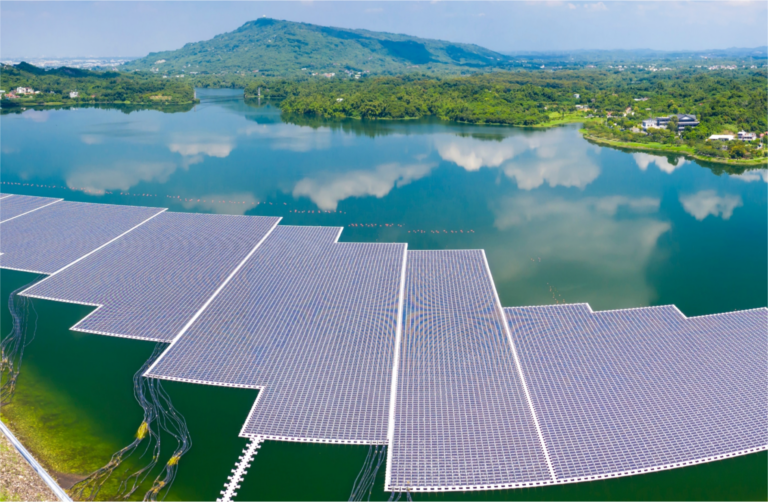
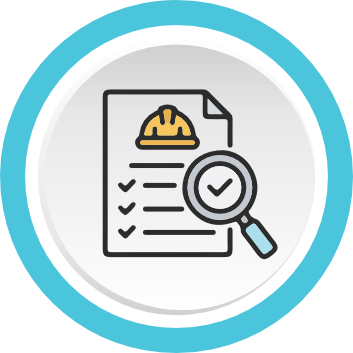
Preventative Maintenance
Regular thermal inspections can identify complications early or identify trends in anomaly types over a period of time. This allows for preemptive maintenance.
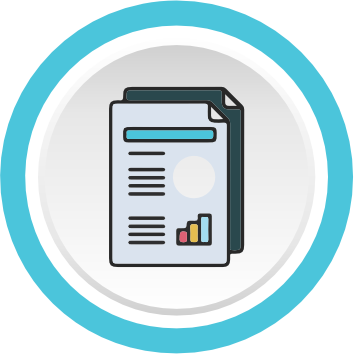
Data Analytics
The data collected from thermal imaging inspections can be analyzed to track the performance of individual panels, predicting issues and optimising energy production.
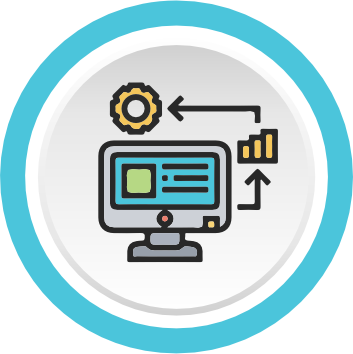
Compliance and Reporting
Drone inspections can provide both visual and thermal data, which can be crucial for compliance reporting, safety checks, and documentation purposes.
WIND FARM TURBINES
Wind farms, with their towering structures and remote locations, require precise and efficient monitoring to ensure optimal performance.
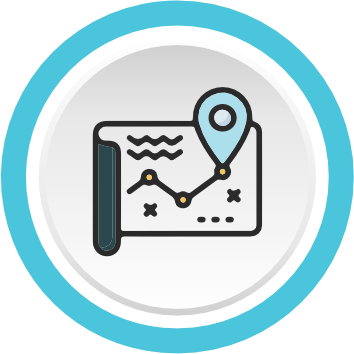
As renewable wind power continues to grow in demand, wind turbine drone inspection will play a critical role in prolonging the service life of wind farms.localised, high-resolution and high-fidelity data.
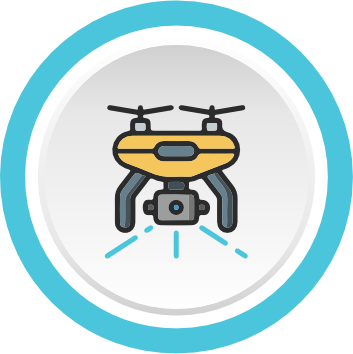
Wind turbines require routine maintenance and inspections to prevent wear and tear, which can reduce the efficiency and lifespan of a turbine’s structural components.
Preventative maintenance
As a proactive maintenance measure, drone inspections of wind turbines can detect early signs of blade delamination and other defects. These inspections gather more comprehensive data compared to traditional methods, leading to faster and more efficient maintenance processes. By using drones, operators can obtain a clearer picture of the turbine’s condition and address potential problems before they escalate.
Drones can reach otherwise inaccessible areas, collecting high-resolution images and thermal readings to pinpoint issues like blade erosion, structural cracks, or alignment problems. This approach allows for quicker identification of faults, reducing downtime and minimising expensive repairs. Additionally, regular automated inspections can be scheduled easily, improving long-term turbine performance and reliability.